Auto Made in Italy, Solare e Low-Cost: Archimede 1.0 – Parte I
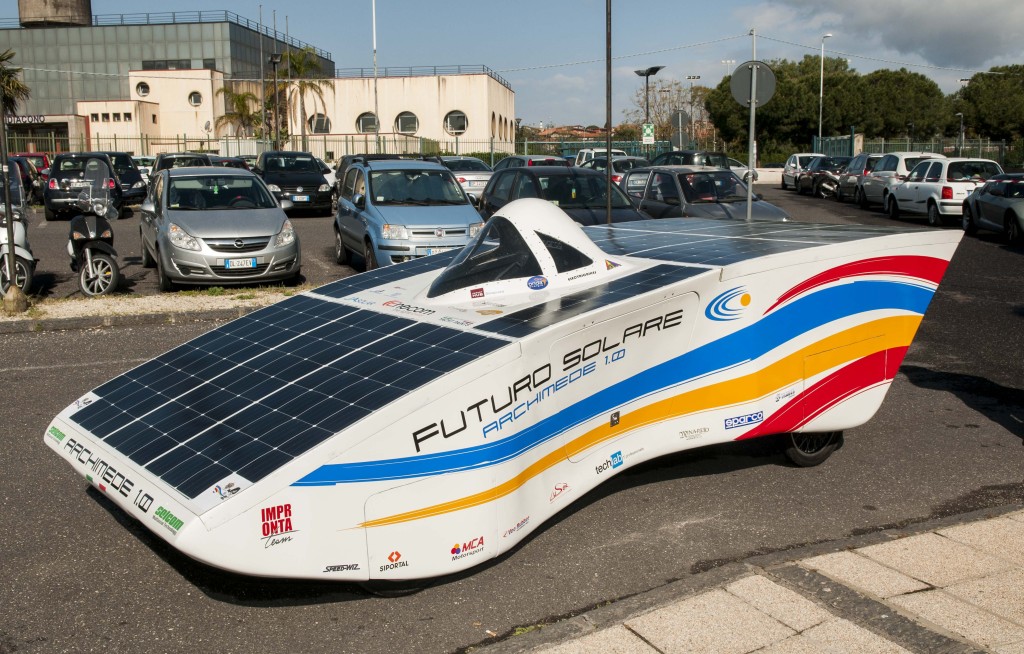
facebook.com/FuturoSolareOnlus
L’Associazione “Futuro Solare Onlus” nasce a Siracusa, in Sicilia, nel 2005 da un gruppo di amici che hanno cominciato a progettare e costruire biciclette elettriche alimentate da energia solare mettendo su un “vero e proprio garage/fab-lab in versione mediterranea”. Stefano Plumeri, studente di ingegneria industriale dell’Università di Catania, è uno dei responsabili del progetto. Con l’aiuto di tutti i componenti del team di Futuro Solare da tempo sta lavorando alla realizzazione del primo prototipo low cost di autovettura elettrica alimentata da conversione fotovoltaica, ARCHIMEDE 1.0! Ecco a voi la prima parte dell’intervista in esclusiva al leader dell’associazione.
Come è nata l’idea di questa Associazione Onlus ingegneristica?
In Università si effettuano ricerche distanti dalla realizzazione e distribuzione su larga scala in quanto l’impiego di materiali e tecnologie sperimentali produce prototipi dai costi proibitivi, quindi difficilmente reperibili sul mercato popolare. L’idea alla base del nostro progetto è anche la mission dell’associazione stessa e si traduce in sperimentazione. Combinando, infatti, in modo differente materiali comuni, reperibili sul mercato e dai costi contenuti, si realizza un prodotto finale alla portata di tutti. Parallelamente alle attività di ricerca l’associazione promuove, inoltre, campagne di informazione, divulgazione e sensibilizzazione focalizzate sul tema delle energie rinnovabili e della mobilità sostenibile, in particolar modo nelle scuole.
Da un punto di vista pratico come siete arrivati alla costruzione del prototipo di Archimede 1.0 e a quali obbiettivi vi siete ispirati in fase di progettazione?
La realizzazione del prototipo Archimede 1.0 ha seguito un iter di quattro fasi progettuali:
- Ricerca e studio di materiali applicabili allo sviluppo di telai e componenti meccanici strutturali del prototipo leggeri resistenti e riciclabili;
- Ricerca e studio di sistemi di recupero dell’energia cinetica e termica;
- Studio e ricerca di architetture aerodinamiche per realizzare la scocca del prototipo;
- Ricerca e studio in campo elettronico per realizzare controller e sistemi di gestione dell’energia ad alta efficienza.
Fornire un’ampia superficie esposta all’irraggiamento solare diretto per l’istallazione delle celle solari, riuscire a utilizzare materiali di uso comune leggeri e resistenti alle sollecitazioni e tecnologie a basso costo con un elevato indice di riciclabilità sono stati i principali obbiettivi ai quali ci siamo ispirati durante la progettazione.
Sono certo che avete affrontato non poche sfide. Quali le più importanti?
Sì, è vero. In fase realizzativa abbiamo dovuto affrontare numerose sfide. Ad esempio rientrare nel budget iniziale che ci eravamo prefissati per la realizzazione del veicolo – 15.000 €; gestire e ottimizzare la potenza ricavata dai pannelli fotovoltaici e cercare di rendere il sistema costruttivo il più semplice possibile.
Quanto tempo necessita l’intera realizzazione del veicolo?
Dal momento della progettazione e verifica dei dati su cad e software di simulazione fino alla realizzazione del veicolo sono stati necessari quattro anni di studi e lavori.
Ci descrivi i materiali scelti per Archimede 1.0?
Il materiale utilizzato per la realizzazione della scocca è stato ideato e brevettato all’interno della nostra associazione ed è un composito costituito da fibra di carbonio, fibra di vetro e kevlar; all’interno di questo “sandwich” è presente un’alveolare d’alluminio che garantisce una maggiore rigidezza del materiale. Il telaio è stato interamente realizzato in alluminio scelto non solo per la sua “leggerezza” ma anche perché non soffre del problema della ruggine e dell’indebolimento tipico delle zone interessate dalla saldatura.
A cosa vi siete ispirati per l’aerodinamica?
Il prototipo è lungo 4,5 m e largo 1,8 m e offre 6 m2 di superficie per le celle fotovoltaiche installate nella parte superiore della vettura. L’aerodinamica del veicolo s’ispirata al profilo alare degli aeromobili ed è stata studiata per minimizzare il cx tramite simulazioni e verifica dei risultati in galleria del vento mediante una prototipazione 3D in scala 1:10 in polistirene. Abbiamo progettato il gruppo sospensioni del veicolo tenendo conto dell’impiego esclusivo in strade asfaltate. Sono state utilizzate due differenti soluzioni per anteriore e posteriore. Per il gruppo sospensioni anteriore, la nostra scelta è ricaduta su un sistema a quadrilatero deformabile mentre per le sospensioni posteriori ci siamo ispirati ai forcelloni oscillanti bi-braccio simmetrico di derivazione motociclistica.
CONTINUA L’INTERVISTA QUI!